Design Sprint: Developing a Cost Reduction Strategy for the Aerospace Industry
Duration: July 2018
Role: UX/UI Designer
Challenge
Create a prototype for an innovative system that leverages black box data from aircraft to monitor and analyze operations, generating insights to optimize aircraft performance. The system should provide information on more efficient taxiing practices and prevent excessive wear on components. With a more informed and proactive approach, the goal is to reduce fuel consumption, minimize aircraft wear, and ultimately lower operational costs.
My role
In the Design Sprint workshop, I worked with a multidisciplinary team consisting of seven aerospace engineers, a graphic designer, a developer, and two facilitators. My role as a UX Designer was to assist in the facilitation of the workshop and in the creation of the final prototype, which was to be presented at an aerospace exhibition.
Problem
Airlines face high costs due to frequent aircraft taxiing, which consumes a significant amount of fuel and causes wear on essential components such as tires and engines. This process not only increases fuel and maintenance expenses but also raises the frequency at which parts need to be replaced, thus driving up overall operational costs.
To reduce these costs, it is crucial to implement stringent maintenance practices and pilot training, focusing on taxiing efficiency and proper inspection execution.
About the project
Process
Given the limited time for prototype development and the extensive technical content to be explored, we decided to adopt the Design Sprint approach. The goal was to create something that clearly and effectively presented the proposal, allowing us to showcase it at a renowned aerospace exhibition to gather feedback and attract potential clients. The workshop was conducted over 4 days and followed a structured process to ensure effective results.
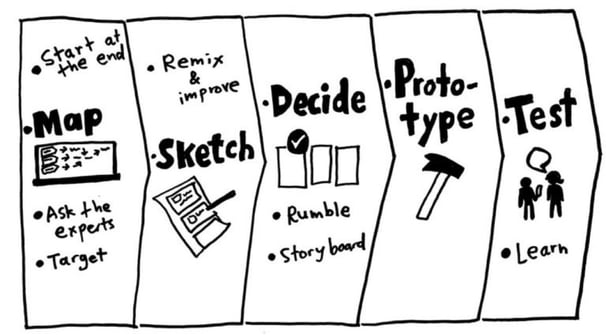
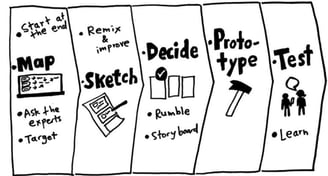
Understanding
The first day of the Design Sprint was quite intense. Even with my prior experience in aerospace projects, the topic at hand was new to me. We started with presentations and extensive discussions to clarify the problem, understand how operations had been functioning up to that point, and explore scenarios that could be incorporated into the prototype to highlight the competitive edge desired by the experts. We identified three main modules that the system should include, focusing on their features and significance.
This day was challenging due to the large amount of information and the complexity of the subject. During the sessions, I observed and noted several issues that remained unresolved, aiming to address them on the following day.
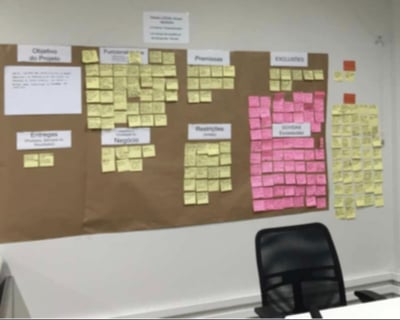
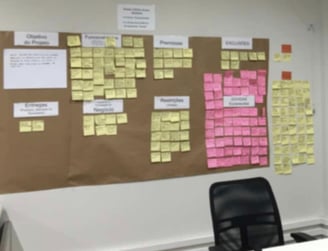
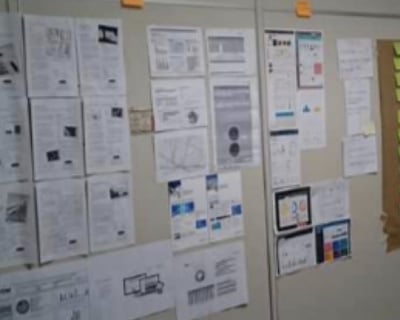
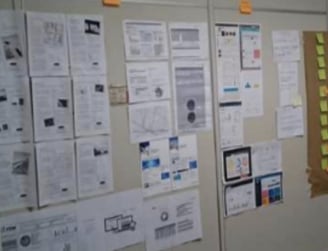
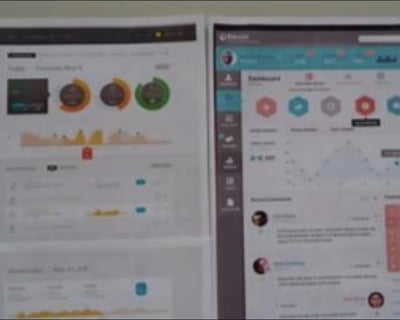
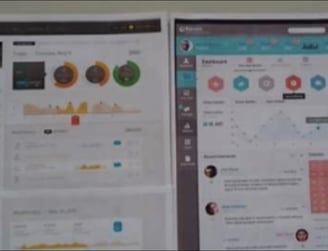
Sketch
The second day of the Design Sprint was divided into three stages. In the first stage, we addressed and clarified any questions from the previous day and were shown benchmark images to inspire the next phase of the day, which involved sketching out ideas for the system on paper.
I, along with the other participants, actively engaged in this stage, sketching and representing my understanding of the project. The outcome of this phase was quite interesting, as the ideas from participants were notably diverse and creative.
In the third stage of the day, each participant had the chance to explain and defend their work, presenting the ideas they developed and discussing their approaches.
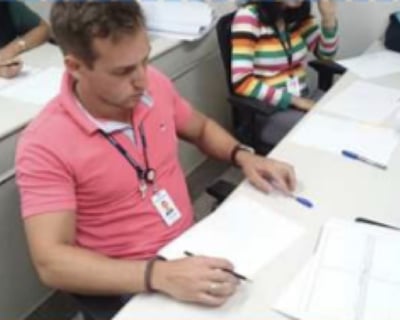
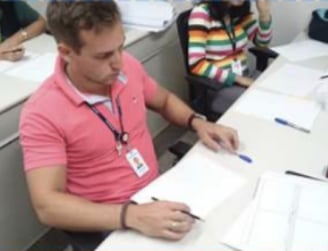
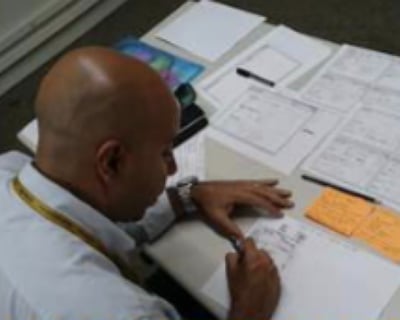
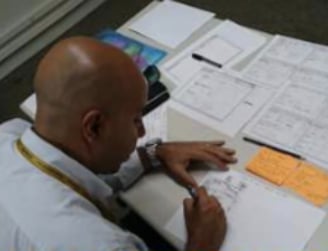
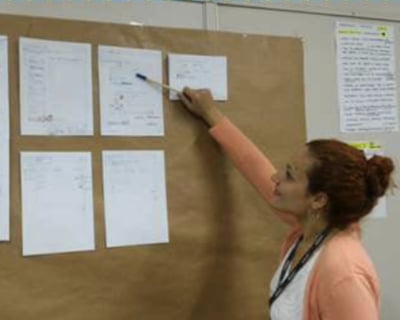
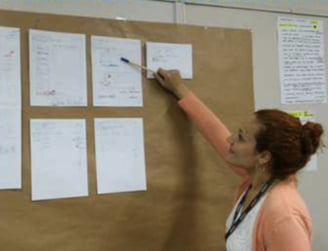
Decide
On the third day of the Design Sprint, we started the morning by voting on the options created. The goal was to decide which elements would be included in the initial prototype. This prototype needed to feature two screens with graphs, descriptions, and a minimum of interactions so we could validate the idea on the fourth day, which would not be the next day, but rather the next week. This way, the interface would be able to work better.
Earlier in the morning, I began creating a flow for the scenario defined by the experts to facilitate the prototyping process. I then started designing the wireframes that would serve as the foundation for the prototype. By the end of the afternoon, I was able to validate the initial idea with the workshop participants, gathering valuable feedback for the next steps.
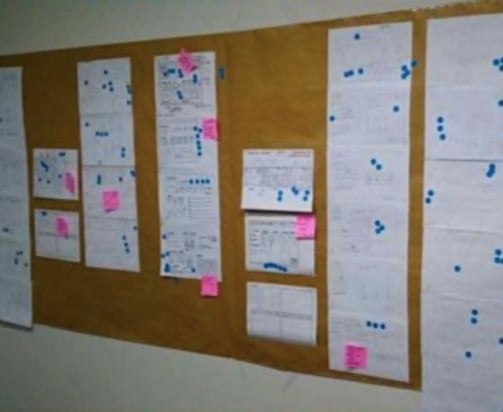
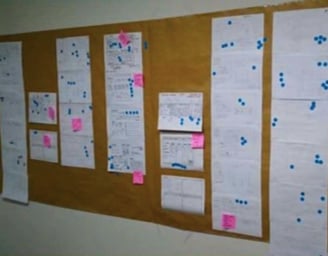
Prototype e Validation
The fourth day was quite busy. I completed the prototype, which consisted of two screens with various graphs displaying an overview of aircraft consumption, safety, and wear. The prototype was created using a visual identity already employed in the company's projects to streamline and expedite the creation process. The benchmark and prototype creation took 2.5 days.
In the afternoon, the prototype was presented to a pilot, four engineers, and a person from the sales department on a tablet. One of the specialists and I introduced the prototype’s objective and asked them to perform three specific tasks.
Overall, everyone was able to complete the tasks with ease. We made some content improvements based on the feedback received to enhance the product’s value proposition.


Learnings and results
After the Design Sprint, we successfully presented the product idea at a pilots' event, confirming the design's effectiveness. The 4-day sprint was brief, and we had to realign our objectives midway through the week to ensure progress.
I managed to get some additional time between the 3rd and 4th days of the workshop to work on the interface. The prototype refinement took an extra week, during which I stayed at the location with the key stakeholders. This allowed us to validate every detail with potential customers and gather valuable feedback.
The prototype presentation at the aerospace fair was highly successful, and the project moved forward. I continued working with the team of specialists on the complete prototype for the system's development.
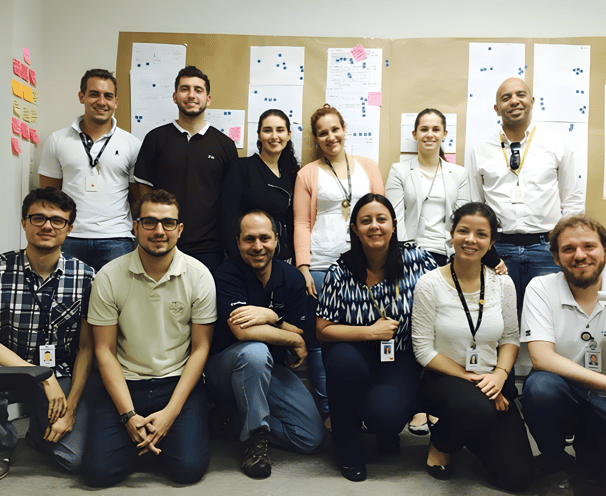
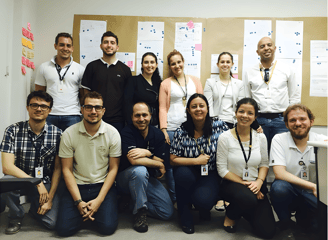